IFP Depth and Pressure Explained
What is an IFP in a Shock, and Why Does Its Depth and Pressure Matter?
When it comes to suspension performance, understanding the role of the Internal Floating Piston (IFP) is key. This small component plays a crucial role in separating oil and gas within the shock’s chamber, allowing consistent damping performance and enhancing ride quality. However, its purpose goes beyond separation—the IFP also accommodates for the displaced oil as the damper shaft plunges deeper, preventing hydraulic lock and ensuring smooth suspension travel.
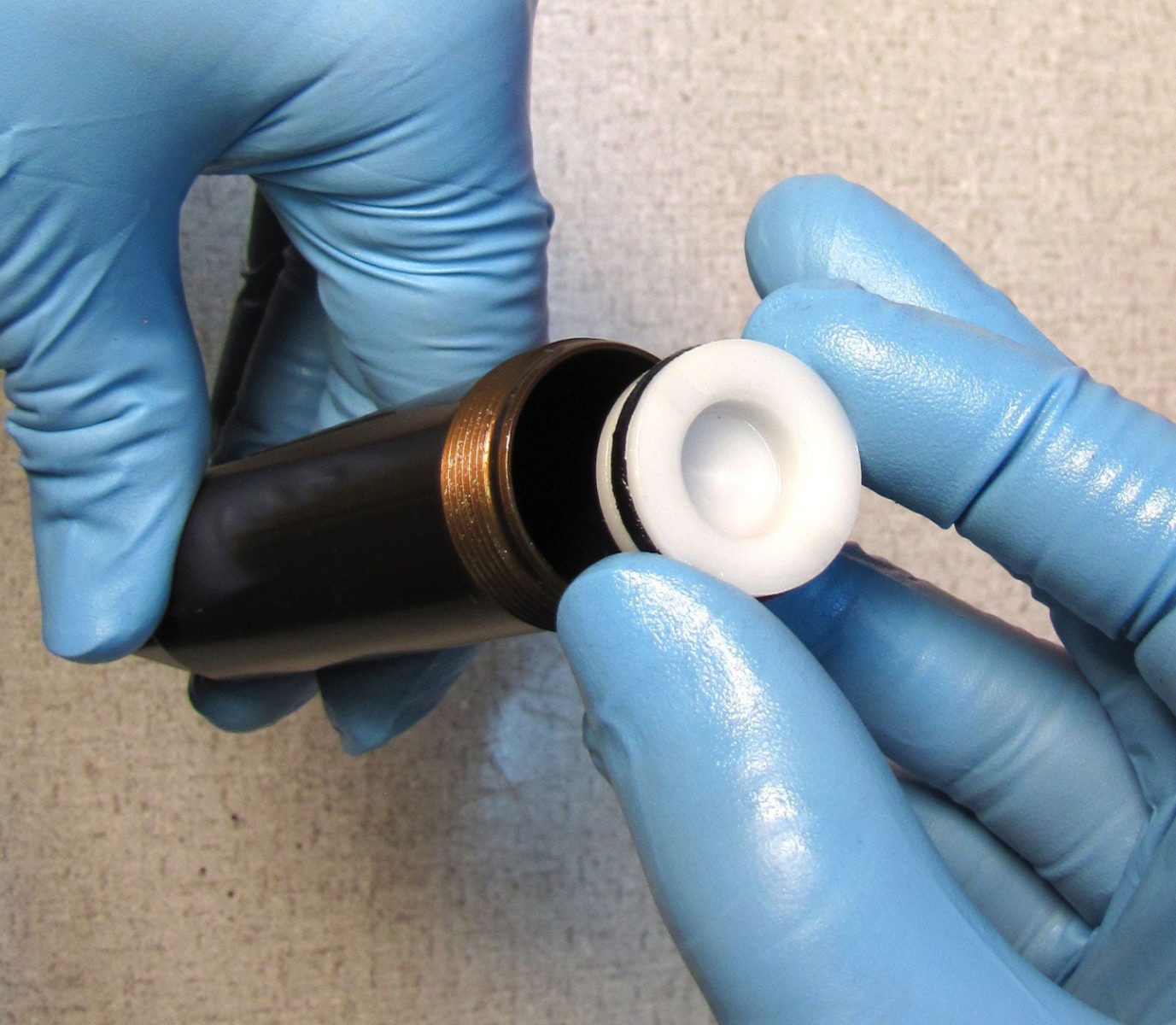
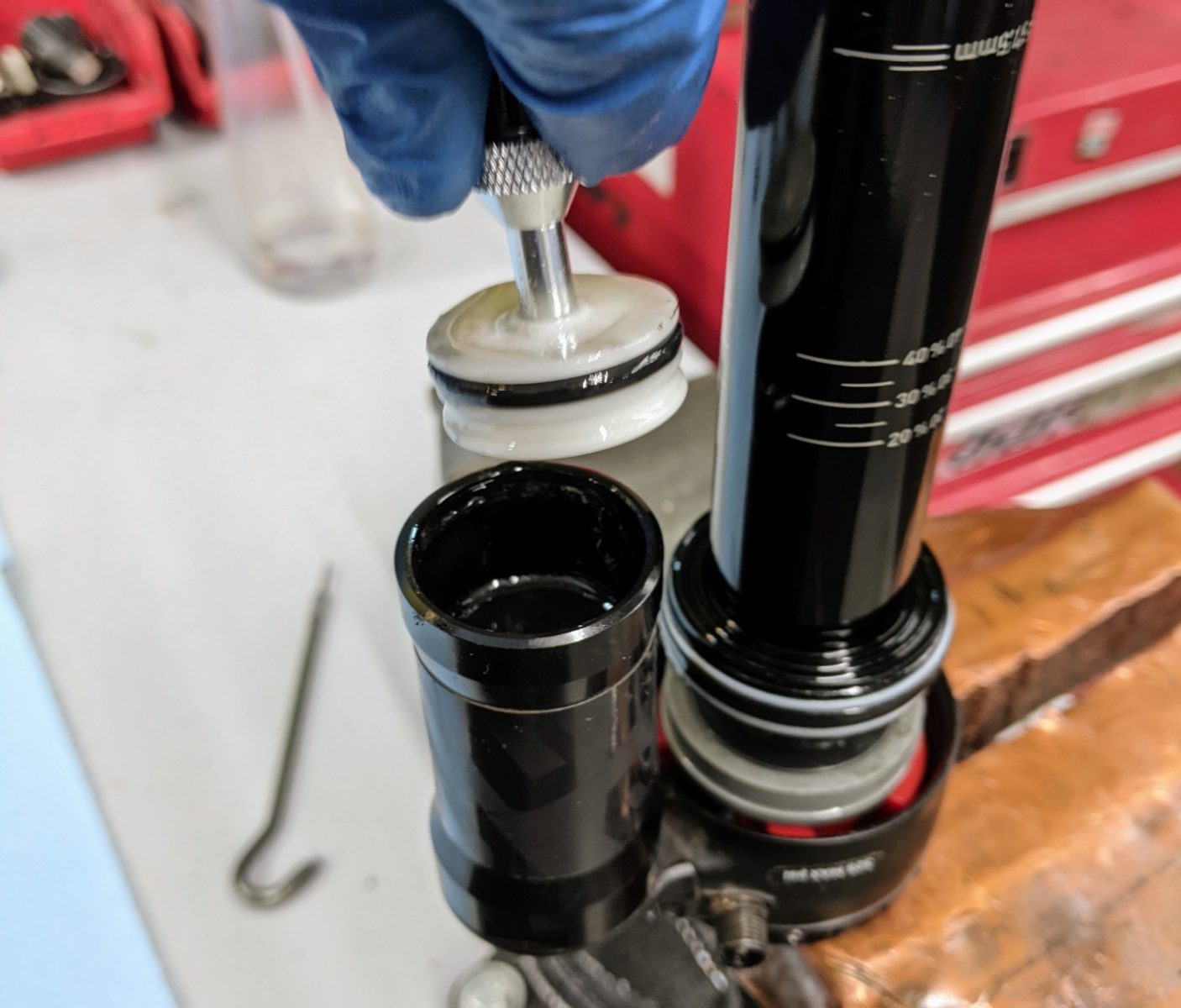
The Role of the IFP in Rear Shocks
The IFP’s primary role is to act as a barrier, separating the shock’s oil from a pressurized nitrogen gas chamber. By keeping the two distinct, the IFP prevents the oil from aerating or mixing with the gas, which could otherwise lead to erratic damping and loss of shock control. Additionally, the IFP provides a critical function by compensating for the increase in internal volume when the damper shaft compresses. As the shaft plunges into the shock body, the displaced oil volume needs somewhere to go; the gas-filled IFP chamber absorbs this displacement, maintaining smooth, predictable shock performance.
The Importance of IFP Depth
When discussing IFP depth, what we’re really considering is the volume of the separate gas and oil chambers within the damper. The correct depth ensures proper oil displacement while maintaining adequate space for the gas chamber. If the gas chamber is too small, there won’t be enough room for oil displacement, which can cause hydraulic lock and reduce the shock’s travel, making it feel harsh or unresponsive. On the other hand, if the gas chamber is too large, the oil volume is reduced, which diminishes resistance and can lead to premature bottoming out under high loads, compromising performance and control. Balancing these chamber volumes is essential for achieving consistent damping and optimal shock performance.
Why IFP Pressure Matters
The IFP pressure plays a critical role in controlling the flow rate of oil between the compression and rebound circuits, which affects the shock’s response during both phases. Higher pressure can result in quicker, more controlled damping, providing a more responsive shock, especially on aggressive terrain or hard landings. Lower pressure allows for a softer, more compliant feel, but too little pressure can lead to sluggish damping, resulting in a “mushy” response and increased risk of bottoming out. While the spring primarily supports the rider’s weight, the IFP pressure fine-tunes the damping characteristics, ensuring the shock responds appropriately to the forces acting on it.
This also brings us to the topic of cavitation, a phenomenon that can compromise damper efficiency, durability, and overall shock performance.
The Importance of the IFP in Preventing Cavitation in Rear Shocks
By maintaining internal pressure within the damper, the IFP is also able to counter cavitation. Cavitation occurs when low-pressure zones form in the shock, causing gas bubbles in the oil. These bubbles can collapse violently under compression, leading to inconsistent damping, reduced shock control, and potential internal damage over time.
By keeping the gas chamber pressurized, the IFP fights cavitation by ensuring that the oil pressure remains stable and bubbles are prevented from forming. This helps to maintain consistent damping performance, even during aggressive riding where rapid compression cycles might otherwise lead to cavitation.
Cavitation’s Effect on Shock Performance
Cavitation in the shock fluid can have detrimental effects, such as:
- Inconsistent Damping: Cavitation creates gaps in the fluid, leading to unpredictable damping response and less control.
- Internal Wear: Cavitation can damage the shock over time, increasing maintenance needs and shortening lifespan.
Correct IFP settings help prevent cavitation, keeping your shock in top shape.
Design Considerations for IFP Depth and Chamber Pressure
When selecting IFP depth and chamber pressure, suspension engineers take several key factors into account to ensure both performance and reliability. They first evaluate the oil displacement volume needed to accommodate the damper shaft’s movement between fully extended and fully compressed positions, ensuring the system can handle the resulting pressure changes without cavitation. They also calibrate the valving circuit flow rates to control the oil speed through the damping valves, which influences shock response across different speeds and terrains. These factors are balanced with other elements like seal friction (stiction) and spring rate, which together shape the ride characteristics, helping achieve an ideal balance of stability, comfort, and performance in dynamic conditions.
In addition to these considerations, engineers account for thermal expansion of both gas and oil, which can affect shock performance as temperatures fluctuate during use. They also consider the gas spring effect, where IFP pressure introduces a minor spring-like force that subtly alters ride characteristics. This effect is balanced with other damping properties to ensure a predictable response. Additionally, engineers must address gas permeability through seals, as gas loss over time can reduce IFP effectiveness, particularly in high-performance or long-travel shocks.
Conclusion
Understanding the IFP’s role and why depth and pressure settings matter is essential for anyone working on rear shocks. Properly set IFP specifications maintain balance, control, and comfort across any terrain. Experienced suspension technicians should check out our helpful cheatsheets to quickly and efficiently find the manufacturer’s recommended depth and pressure settings for most popular shock models.